745 TurboGreasel
New member
- Joined
- May 10, 2005
- Location
- Freedom CA
They say you have to pull the head, and pay a million dollars, not so fast!
Drilling, and easy outs, I pretty much don't even try.
Here one method using the welder is described in post #6.
I do it a little different.
Here is a typical broke a bit below deck manifold stud.
Get any oil, flammables, and other contaminates off the immediate area.
I taped off the neighboring areas to reduce cleanup from MIG spatter, because I am a flux core whore.
I go pretty high power, not much wire, bigger fastener, more power.
This is a portable 110V unit running 032 flux core wire.
Now you are set
Now you are set up, take a nut about the size of the broken fastener in you Vice-Grips, and hold it flush with the hole.
Aim your MIG through the nut(down is easiest, but not mandatory, upside down sucks balls) and fire away.
Theory; Any fastener that is glowing cherry red will deform enough to unthread with the greatest of ease. That state can be a bit hard to achieve when a bolt is broken inside your motor, but each heat cycle will loosen its grip a bit.
Weld only sticks to hot metal, and the block is a huge sink. This works in our favor, we can add material to the bolt, and being liquid,it builds up to the existing threads, but doesn't bond to them. Heat doesn't want to jump the microscopic gap at the edge of the thread, so most of it goes down the fastener, making our job easier.
Burn into the broken face of the fastener, up to the deck, then you want to circle a bit, filing the nut, and doming the top to send as much heat as possible down to the threads.
Quick, while it is still glowing give it a wiggle, and unthread it if you can.
Sometimes I use the 'Grips, sometimes a ratchet or impact.
If the weld just breaks off, don't worry, you just added 100* to that nasty bolt, and the next nut will add 100 more. The heat differential will pull PB down the threads if you want to try that.I don't think I've ever used more than 7 nuts on one hole.
Yay, unthreading
Carnage.
Aluminum goes the same, most times you don't even need to rethread the hole.
Flanged nuts are nice to use, because they hold themselves flat a little easier.
Sometimes I'll taper the inside of the nut with a drill so I don't have to shoot such a narrow tunnel.
Why do studs fail? More theory;
A stud should be threaded in, then backed off 1/16 turn.
Then the nut is tightened over the part to provide clamping force.
Clamping force necessarily equals stretch on the stud
As an exhaust manifold heats up, it grows longer, the through holes may jam up on the stud, adding shear force to the already (however slightly) stretched stud, and POP, out of the blue, you are missing half a stud, or a permanent weak point is created where the part threaded into the head couldn't move.
Later, When you go to remove the nut, dissimilar metals have bonded after thousands of heat cycles, somebody forgot to use anti seize,and/or that weak spot is still there, at the narrow spot a thread or 3 in.
Use copper or brass nuts on your exhaust even though they cost more.
If you overtighten the nut, and break a properly installed stud, all tension is released, and you can push a pencil eraser down the hole, and spin the broken nub out....
If the stud or bolt was run to the bottom of the hole, and given another 1/4 turn, not so much. The bottom can no longer turn, the top of the thread is the weak point, and twists off. Now there is no handle, and the nub is seriously jammed into the hole. You can heat it till it changes shape, or you can jumpstart things a bit by taking a hammer(and a punch if appropriate), and driving the stuck fastener straight into the hole.
1 This sends a seismic shock through an bond that may have formed along the threads,
2 both male and female threads are momentarily distorted, but they only spring back part way, threading action just got smoother.
3 the bottomed part of the fastener is mushed against the end of the hole, but since it doesn't spring back 100%, the jam is not as strong as it was.
4 Threads area ramp twisted into a circle,the fastener can't go far from your many hammer strike, but on recoil, it sees ramp, and wants to unwind.
This works on all stuck nuts and bolts. Hammer a tight lug nut straight at the wheel for 15 minutes, and you will find it is not even finger tight.
Disclaimer;
If you are a bonehead, and light yourself, your car, or your neighborhood on fire, I am not liable, responsible, or even sympathetic. Use common sense, and don't get in too far over your head.
If I save you $1000, you can PP me a 6pack
Good luck!
Drilling, and easy outs, I pretty much don't even try.
Here one method using the welder is described in post #6.
I do it a little different.
Here is a typical broke a bit below deck manifold stud.
Get any oil, flammables, and other contaminates off the immediate area.
I taped off the neighboring areas to reduce cleanup from MIG spatter, because I am a flux core whore.
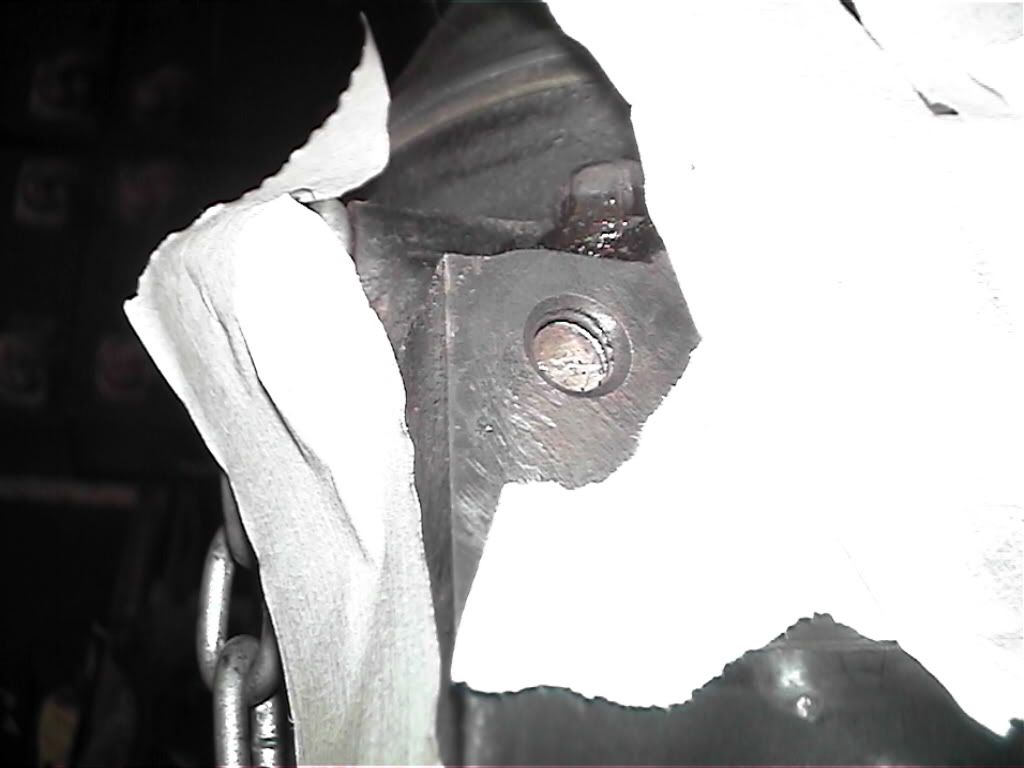
I go pretty high power, not much wire, bigger fastener, more power.
This is a portable 110V unit running 032 flux core wire.
Now you are set
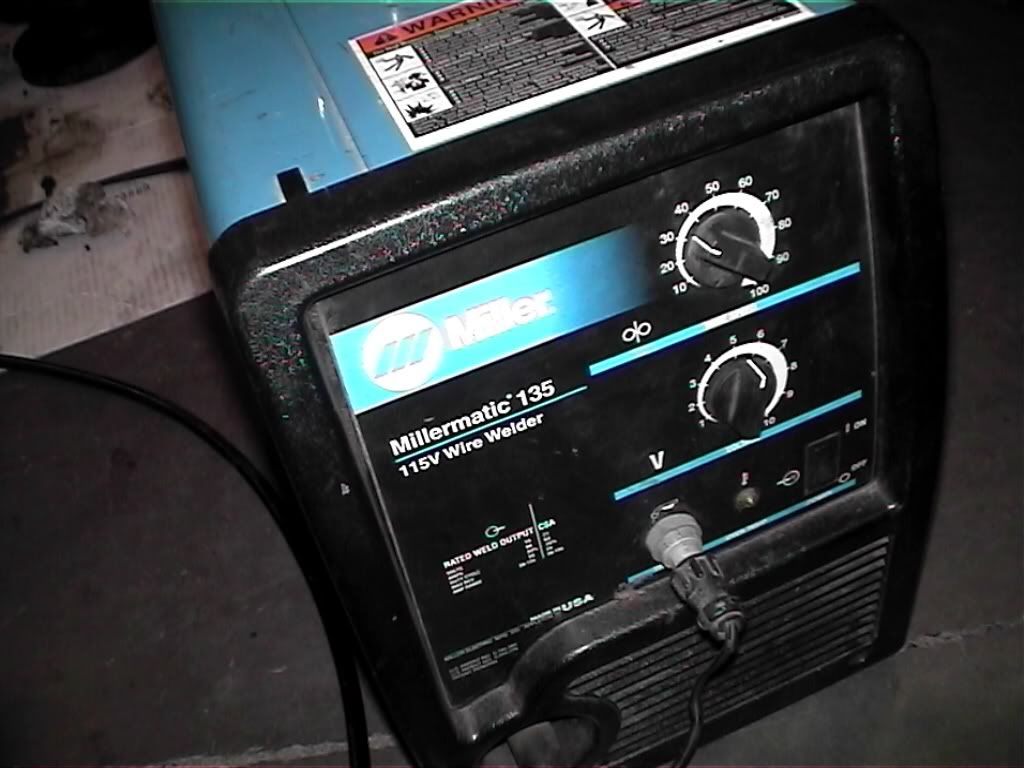
Now you are set up, take a nut about the size of the broken fastener in you Vice-Grips, and hold it flush with the hole.
Aim your MIG through the nut(down is easiest, but not mandatory, upside down sucks balls) and fire away.
Theory; Any fastener that is glowing cherry red will deform enough to unthread with the greatest of ease. That state can be a bit hard to achieve when a bolt is broken inside your motor, but each heat cycle will loosen its grip a bit.
Weld only sticks to hot metal, and the block is a huge sink. This works in our favor, we can add material to the bolt, and being liquid,it builds up to the existing threads, but doesn't bond to them. Heat doesn't want to jump the microscopic gap at the edge of the thread, so most of it goes down the fastener, making our job easier.

Burn into the broken face of the fastener, up to the deck, then you want to circle a bit, filing the nut, and doming the top to send as much heat as possible down to the threads.
Quick, while it is still glowing give it a wiggle, and unthread it if you can.
Sometimes I use the 'Grips, sometimes a ratchet or impact.
If the weld just breaks off, don't worry, you just added 100* to that nasty bolt, and the next nut will add 100 more. The heat differential will pull PB down the threads if you want to try that.I don't think I've ever used more than 7 nuts on one hole.
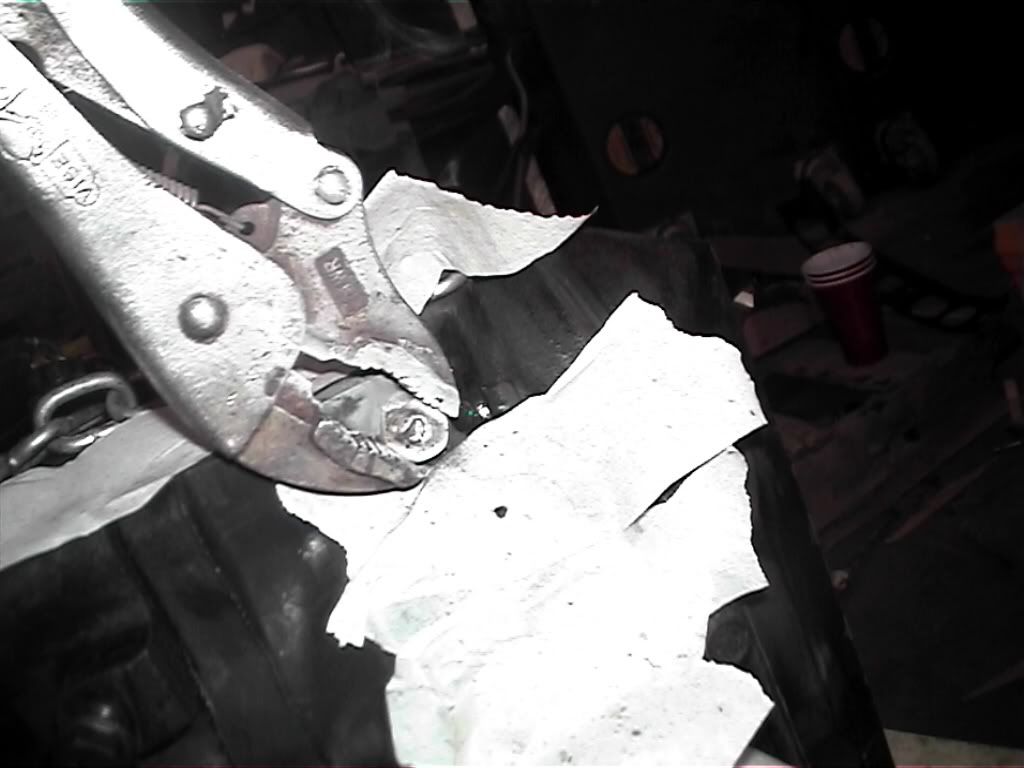
Yay, unthreading


Carnage.
Aluminum goes the same, most times you don't even need to rethread the hole.
Flanged nuts are nice to use, because they hold themselves flat a little easier.
Sometimes I'll taper the inside of the nut with a drill so I don't have to shoot such a narrow tunnel.
Why do studs fail? More theory;
A stud should be threaded in, then backed off 1/16 turn.
Then the nut is tightened over the part to provide clamping force.
Clamping force necessarily equals stretch on the stud
As an exhaust manifold heats up, it grows longer, the through holes may jam up on the stud, adding shear force to the already (however slightly) stretched stud, and POP, out of the blue, you are missing half a stud, or a permanent weak point is created where the part threaded into the head couldn't move.
Later, When you go to remove the nut, dissimilar metals have bonded after thousands of heat cycles, somebody forgot to use anti seize,and/or that weak spot is still there, at the narrow spot a thread or 3 in.
Use copper or brass nuts on your exhaust even though they cost more.
If you overtighten the nut, and break a properly installed stud, all tension is released, and you can push a pencil eraser down the hole, and spin the broken nub out....
If the stud or bolt was run to the bottom of the hole, and given another 1/4 turn, not so much. The bottom can no longer turn, the top of the thread is the weak point, and twists off. Now there is no handle, and the nub is seriously jammed into the hole. You can heat it till it changes shape, or you can jumpstart things a bit by taking a hammer(and a punch if appropriate), and driving the stuck fastener straight into the hole.
1 This sends a seismic shock through an bond that may have formed along the threads,
2 both male and female threads are momentarily distorted, but they only spring back part way, threading action just got smoother.
3 the bottomed part of the fastener is mushed against the end of the hole, but since it doesn't spring back 100%, the jam is not as strong as it was.
4 Threads area ramp twisted into a circle,the fastener can't go far from your many hammer strike, but on recoil, it sees ramp, and wants to unwind.
This works on all stuck nuts and bolts. Hammer a tight lug nut straight at the wheel for 15 minutes, and you will find it is not even finger tight.
Disclaimer;
If you are a bonehead, and light yourself, your car, or your neighborhood on fire, I am not liable, responsible, or even sympathetic. Use common sense, and don't get in too far over your head.
If I save you $1000, you can PP me a 6pack
Good luck!
Last edited: